Embodied carbon
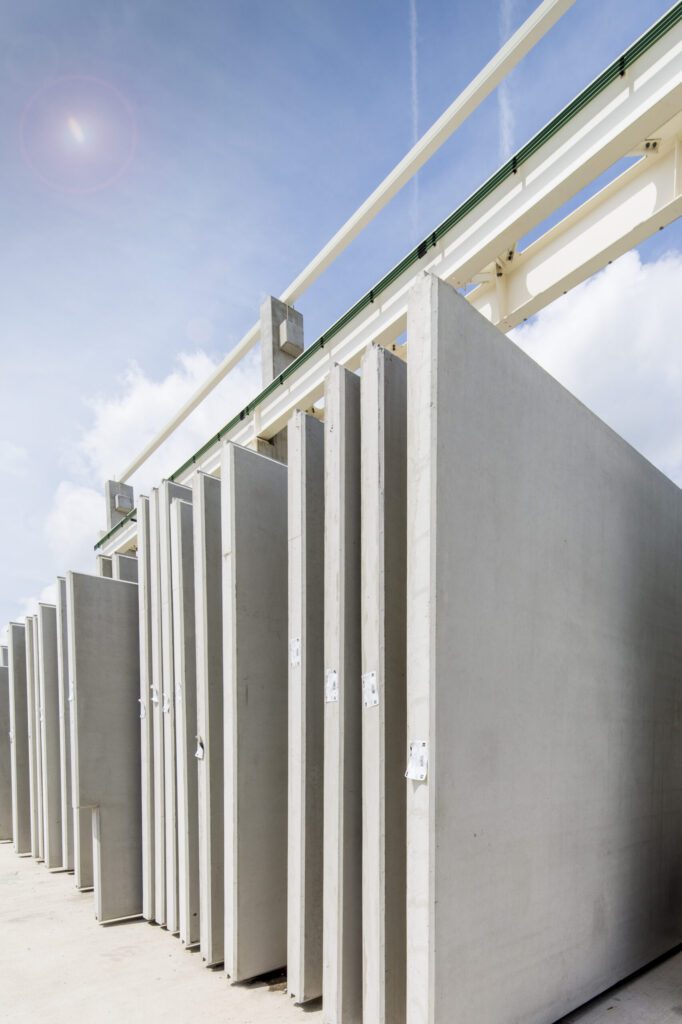
Decreasing the embodied carbon of our buildings
Embodied carbon refers to greenhouse gas emissions generated during the production of building materials and construction including transportation, use phase and disposal.
It is an important factor to consider for sustainable building practices, as it accounts for a significant portion of a building’s overall carbon footprint.
At Cordeel, we are committed to reducing the embodied carbon of our buildings. By carefully selecting durable and sustainable materials, we build future-proof projects for our customers. Parts of the industrial buildings we realise are built with wooden beams. Another important approach is the usage of substitute cementicious materials (SCMs) in our green concrete’s composition.
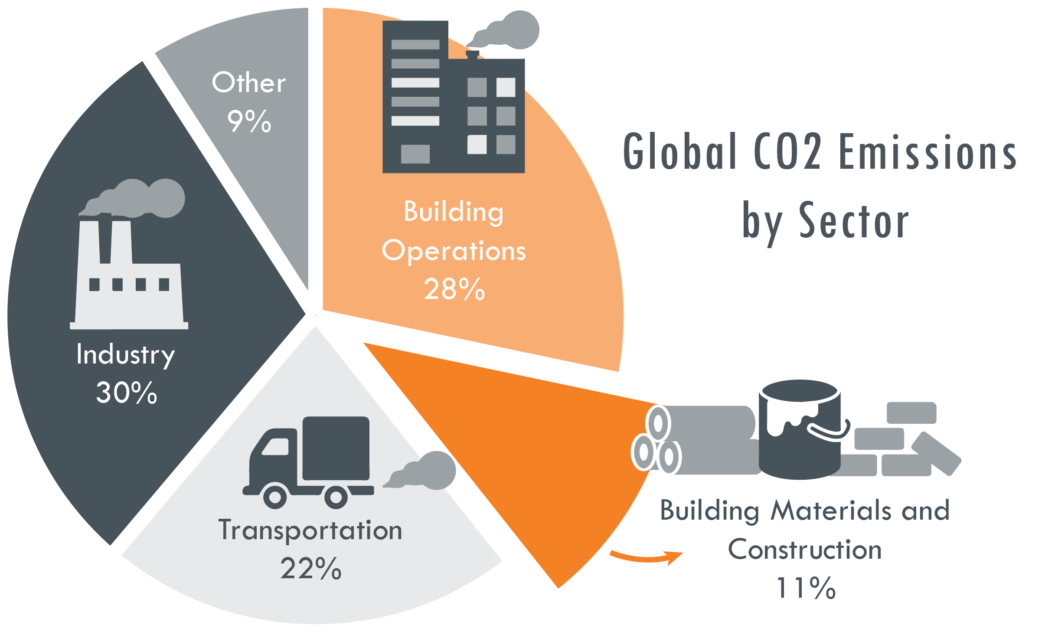
Life Cycle Assessments
We see an increasing demand for LCA’s in tenders which is why we build up in-house knowledge. We are conducting these assessments on product- and building-level using the One Click LCA tool to confirm our assumptions and intentions on reducing their impact.
For our most used precast concrete mix we have conducted a LCA which helps us to continuously improve the formula.
Currently, we’re finishing the LCA of C-battery’s battery modules. We’re also working on the LCA for various other materials, like hemp-based products or plaster.
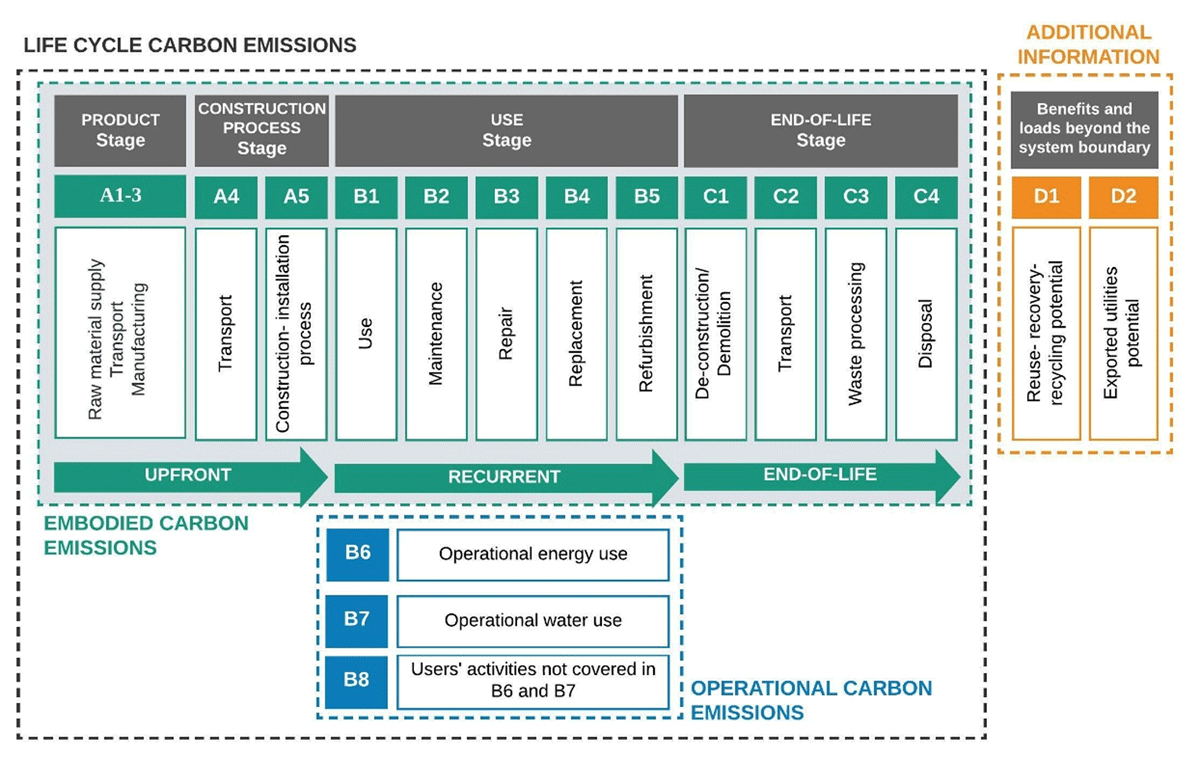
Green concrete
Structural components like columns, beams, walls and floors have a significant impact on the embodied carbon of buildings. We aim to industrialise the building process as much as possible and use concrete precast elements for structural components, prefabricated by C-concrete.
In 2018, C-concrete used 70% CEM I and 30% CEM III cement for our precast concrete elements. CEM I contains 100% cement clinkers which results in significant CO₂ emissions. To reduce these emissions, we made it a top priority to reduce the cement clinker level in the cement compositions that we use at C-concrete.
Over the past years, we have conducted intensive research and testing to develop alternative concrete mix formulas that minimise the use of cement. Our aim is to reduce the use of cement, which is responsible for 7% of the global CO₂-emissions, as much as possible.
“Our ‘green concrete’ initiatives aim to cut embodied carbon in our precast elements by using less and other cement and substitute materials.”
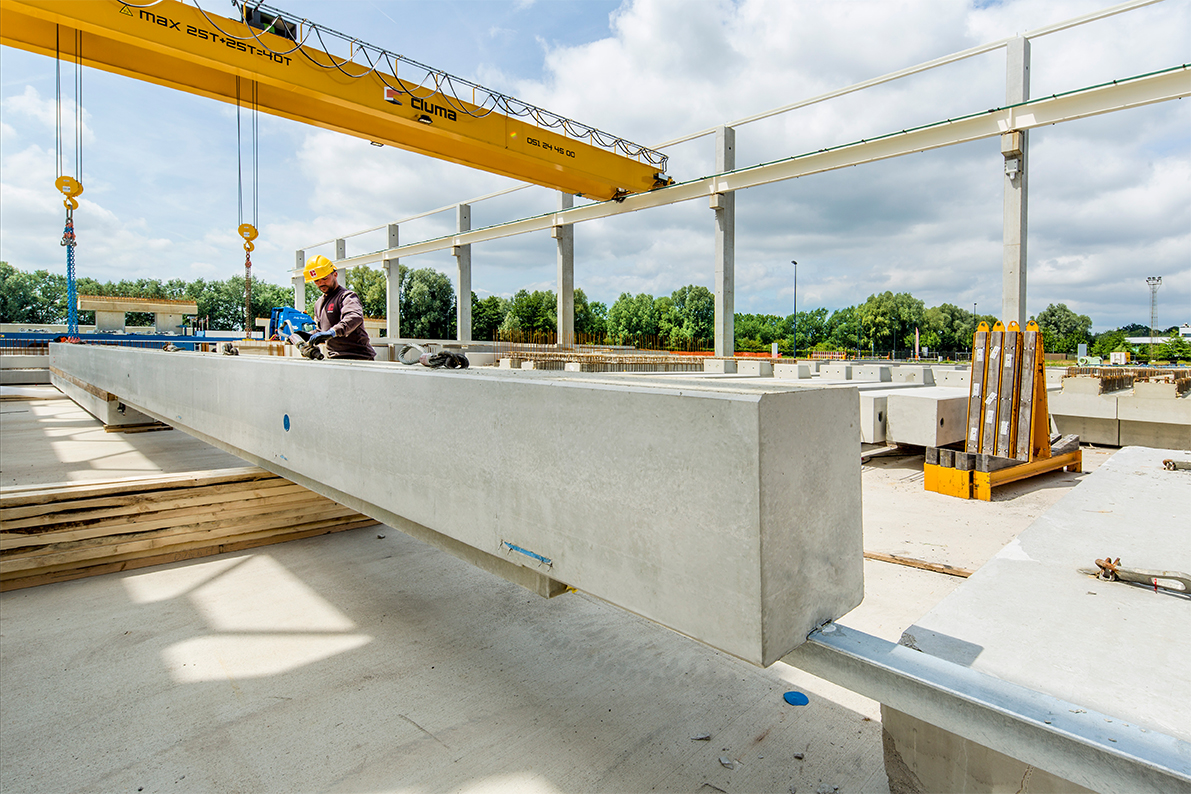
Our current standard formula is still within the BENOR norm, which gives us a competitive edge in the market. Since Q2 2024 we are producing our regular beams, columns and full walls with 100% CEM III/A. This accounts for a reduction of embodied of more than 20% compared to CEM I.
We continue to reduce CO2-emissions by using alternative binders, substitute materials, and additives to continuously adapting the formulas of the different types of concrete we use.
In 2024 we used CEM II/A for the production of white concrete for the first time, which reduced our emissions by 10% compared to CEM I.
We have installed a new silo for blast furnace slags which will accelerate the production of more individual concrete mixes. Blast Furnace slags are recycled raw materials from the metal industry, that are used to substitute cement clinker.
Our granulate recycling installation helps us to recover the granulates from our excessive unhardened concrete, thus reducing our concrete waste and the loss for virgin materials.
Most of our raw materials like sand and aggregates are being delivered by boat to our facility in Temse.
In 2025 we will continue adapting our concrete formulas and further explore the use of secondary raw materials.
Future-proof logistics buildings
In October 2024, Cordeel Group launched NEXUS Logistics, a new modular warehouse concept that combines circular construction with high energy performance.
Drawing on the collective expertise of its subsidiaries and partners, Cordeel delivers tailored logistics facilities that are adaptable, low-carbon and built fast.
The warehouses are designed to evolve with changing business needs, allowing for expansion or reconfiguration without material waste.
The concept prioritises sustainability at every level without over-stretching construction budgets. Bio-based insulation, low-emission steel decks, timber beams and low-carbon concrete reduce embodied carbon by 38% compared to traditional concrete warehouses.
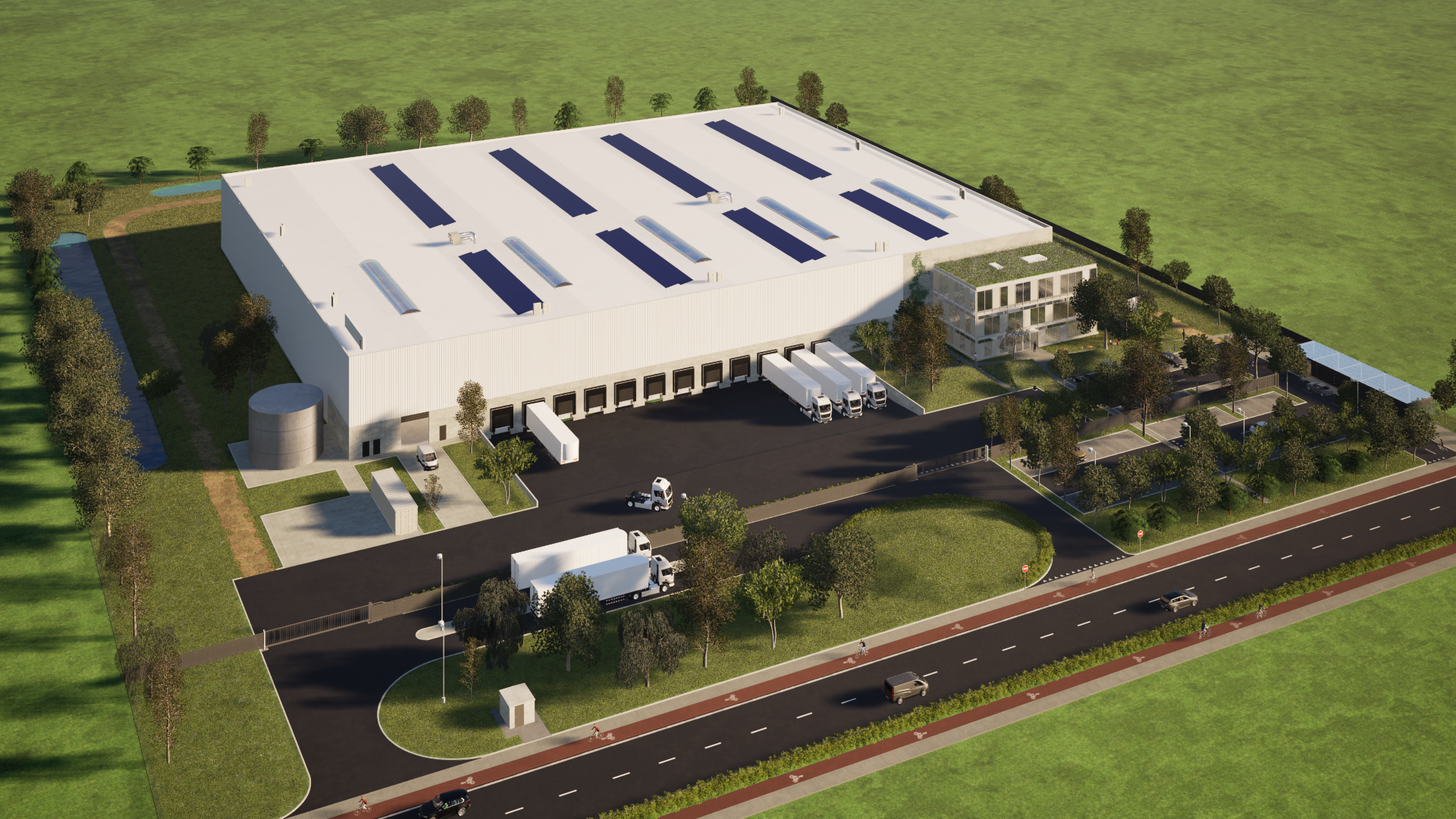
Energy systems are engineered to use 20 kWh per square meter annually – compared to a sector average of annually 70 kWh/m² just a few years ago.
“We not only reduce our customers’ ecological footprint and energy bills, we also make their operations future-proof and ready for the logistical challenges of tomorrow.” Kevin De Hainaut (CEO Cordeel Belgium)
Heat pumps, charging infrastructure, solar panels and optional battery storage are being installed while Energy Management Systems further enhance efficiency and control.
These energetic systems can be offered in an “as a service” approach as well, reducing the CAPEX of the project.
Prefabricated components, a standardized grid and detailed BIM modelling ensure fast construction and smoother project delivery.
Finally, NEXUS Logistics also addresses biodiversity with features like green roofs and adapted landscape design. The outside recreational areas enhance employee well-being, creating a harmonious balance between nature and industry.
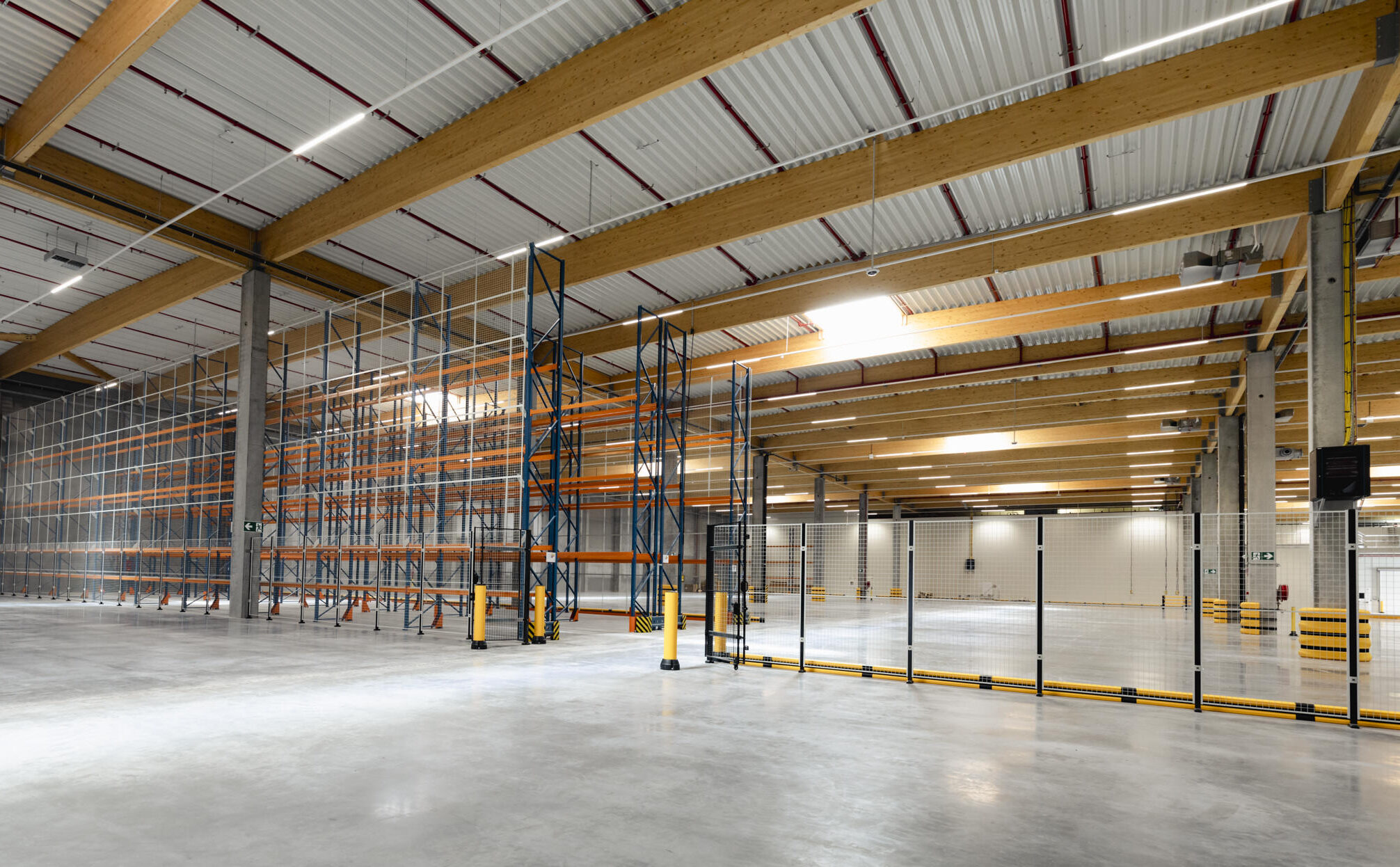
Reconversion projects
In the last years, we are witnessing an increase in renovation and reconversion projects, particularly in Brussels. These projects typically have very high sustainability and circularity ambitions.
Renovating existing structures, rather than opting for demolition and new builds, significantly reduces embodied carbon and need for primary raw materials by maintaining the original structure.
Looking forward, we will continue working on these type of projects, leveraging the strengths of our ecosystem of companies. For some of the current projects we already apply the Heat As A Service concept by C-energy and plan to adopt the ESCO model (Energy Service Company model) as well for future projects. This allows for comprehensive energy performance improvements, ensuring that renovations are not only structurally sustainable but also energy-efficient in the long term.
One of the most compelling examples of this approach is the renovation of the Multi redevelopment, a landmark located in the heart of Brussels. Our construction team realised a BREEAM Excellent certification for the renovation project completed in 2022, with a strong focus on utilising recovered materials.
Oxy: There is a deliberate choice for a thorough renovation, with materials being reused either on-site or elsewhere. The building also distinguishes itself in terms of energy sustainability, including the integration of heat pumps and incorporating solar panels into the facades. The mixed-use building will comprise 43,000m² of offices, a 15,000m² hotel with 316 rooms, and 112 apartments.
Montgomery Square: We started renovating the former RIZIV buildings in Brussels into a future-proof complex with offices, a large park, sports facilities, and other amenities. The 22.000 m² project aspires to reach a number of ambitious sustainability certifications like BREEAM Outstanding, DGNB Platinum and WELL Platinum.
The Ambiorix site in Tongeren is a former military site that is being redeveloped by C-living. The former buildings are renovated step by step, keeping the character in tact. Additionally, we focus on removing the former sealed areas and creating a future-proof and ambitious masterplan that takes into account the biodiversity of the nature reserve “De Kevie”.
Bio-based products made from industrial hemp
C-biotech is currently in the last R&D stages of several bio-based products made from industrial hemp. In the coming months and years we are striving to accelerate the market of these kind of products by introducing hemp wool insulation, wooden sheets, mycelium insulation and C-hemp: the combination of wooden sheets and mycelium insulation that will act as interior wall.
The first products available are acoustic panels made from mycelium and rubberwood, a rest stream from our production at C-wood. Together with our partner Trafiroad, we will install hundreds of traffic poles made from a biocomposite based on hemp.
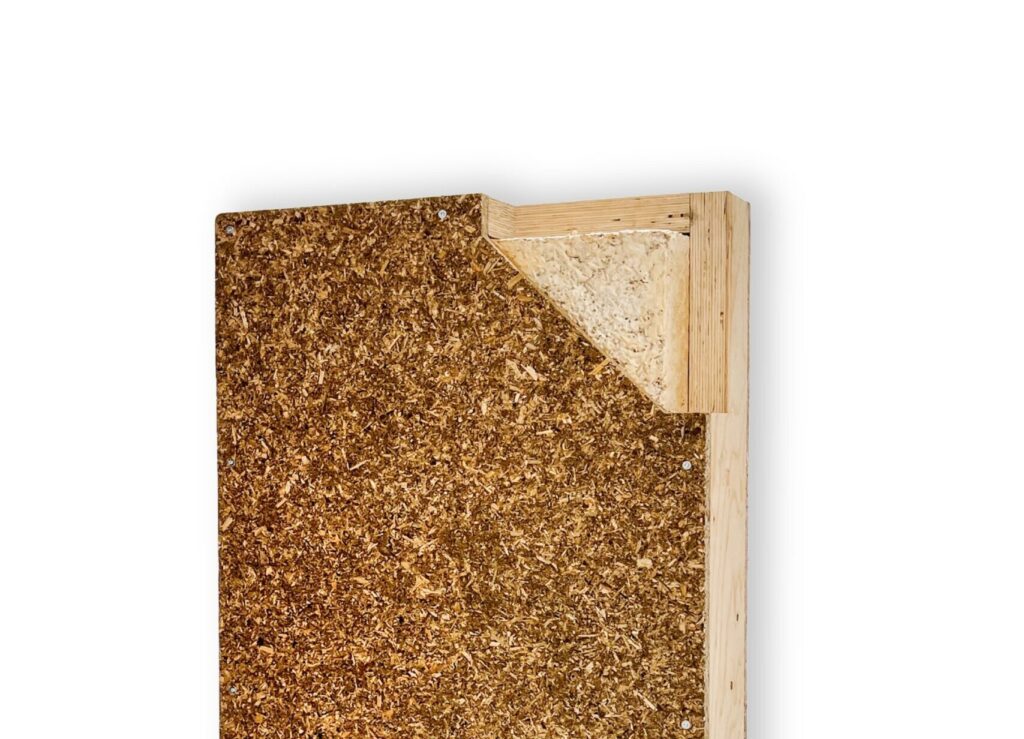
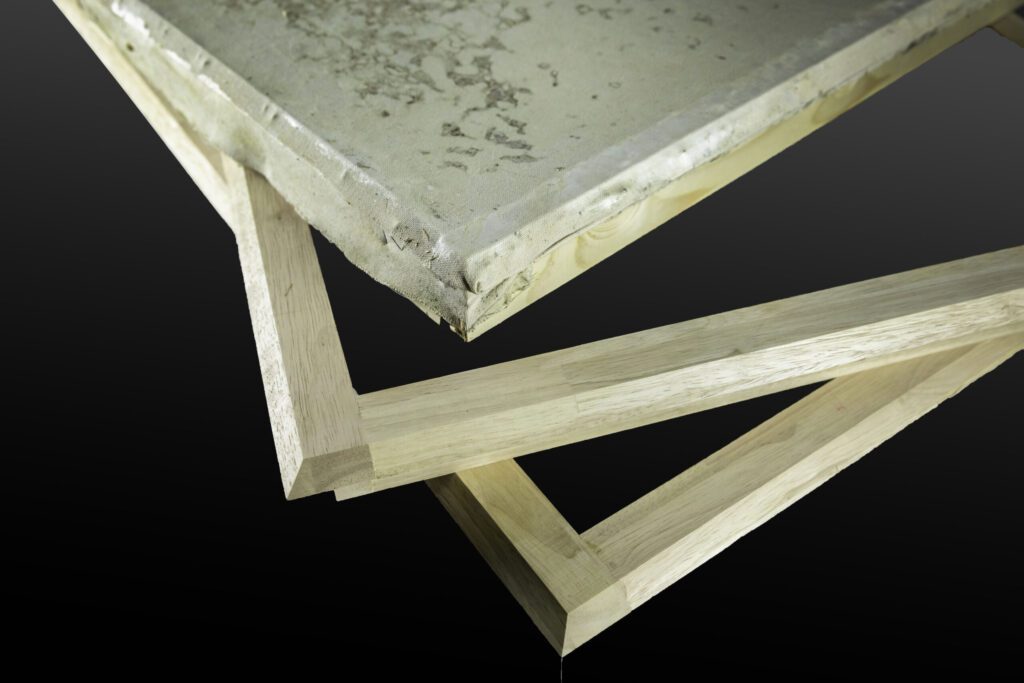
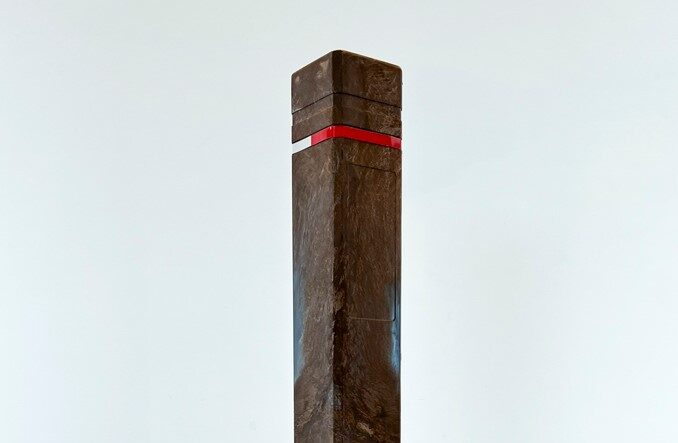
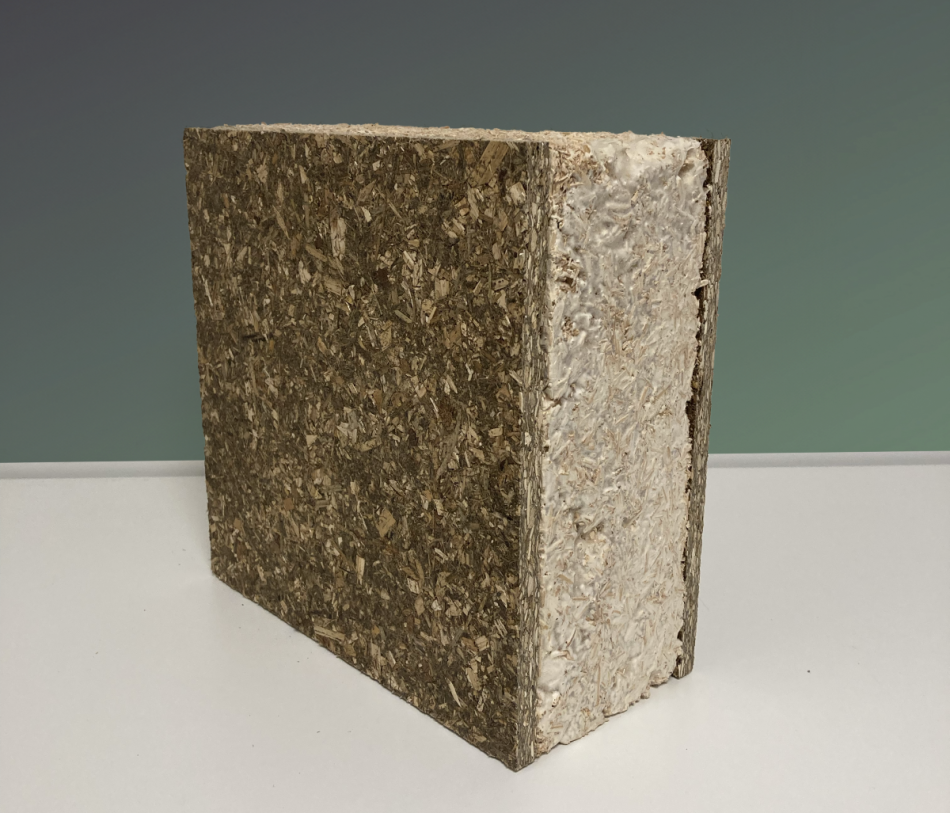
Internal focus groups
The Focus Groups are crucial to improve our impact on Cordeel Group’s most material sustainability matters. They are composed of multidisciplinary teams from different entities.
Green concrete
The focus group “green concrete” is driving the reduction of embodied carbon of our precast concrete production and explores as well the use of secondary raw materials.
Being sponsored by Peter Van Inghelghem (CEO C-production) who is part of the Cordeel Group ExCo, the team receives the necessary support to execute on the quarterly and yearly plans.
Sustainable standardisation of industrial buildings
This focus group is working on improving the standardisation of our industrial buildings. They focus on the reduction of embodied carbon and improving on design for disassembly and other circularity aspects. By making our standardisation for industrial buildings future-proof, we support our customers in their sustainability performance.
The focus group is sponsored by Isabelle Dumon, member of the management team of Cordeel Belgium.