Embodied carbon
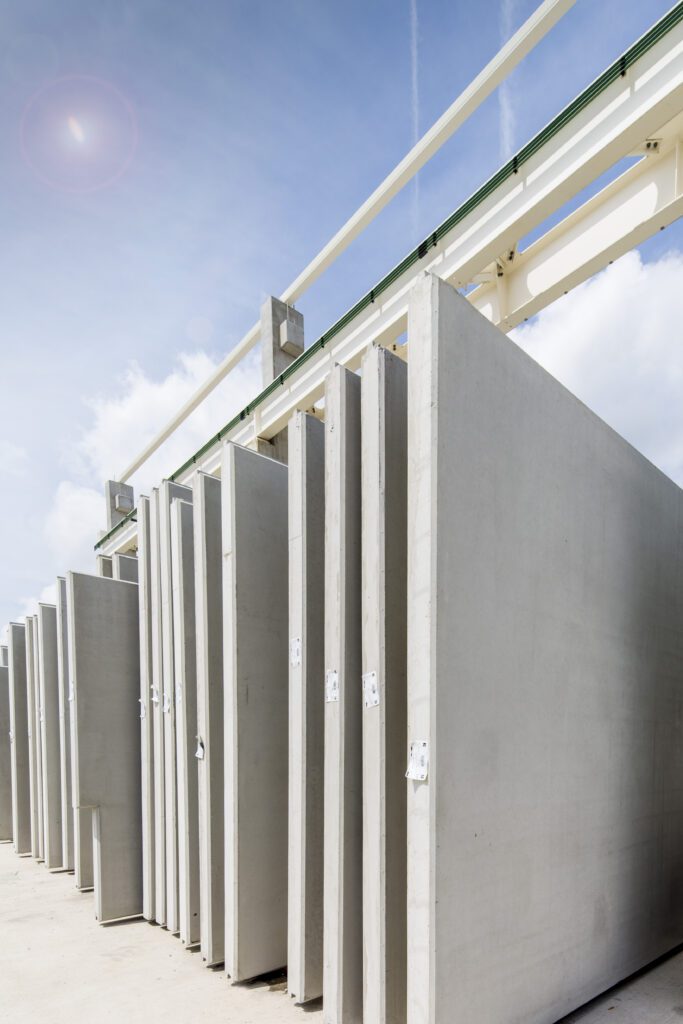
Decreasing the embodied carbon of our buildings
Embodied carbon refers to greenhouse gas emissions generated during the production of building materials and construction including transportation, use phase and disposal.
It is an important factor to consider for sustainable building practices, as it accounts for a significant portion of a building’s overall carbon footprint.
At Cordeel, we are committed to reducing the embodied carbon of our buildings. By carefully selecting durable and sustainable materials, we build future-proof projects for our customers. Parts of the industrial buildings we realise are built with wooden beams. Another important approach is the usage of substitute cementicious materials (SCMs) in our green concrete’s composition.
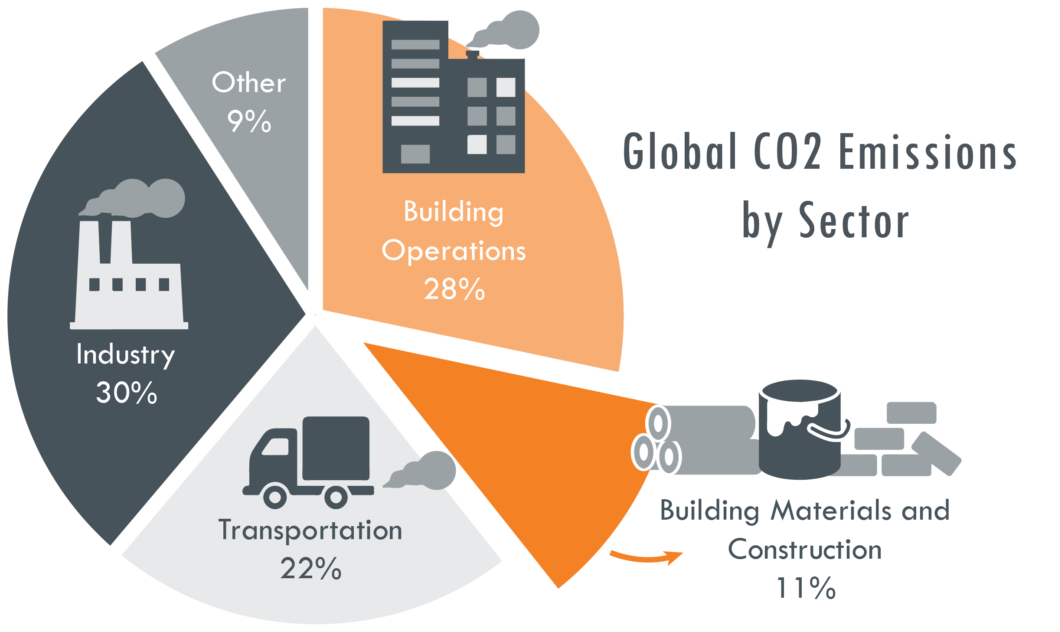
Life Cycle Assessments
We see an increasing demand for LCA’s in tenders which is why we build up in-house knowledge. In the future, we will be conducting more LCA’s on product- and building-level to confirm our assumptions and intentions on reducing their impact.
We have conducted a LCA for our most used precast concrete mix which helps us to further improve the formula. Currently, we’re waiting for the Belgian EPD to be finalized.
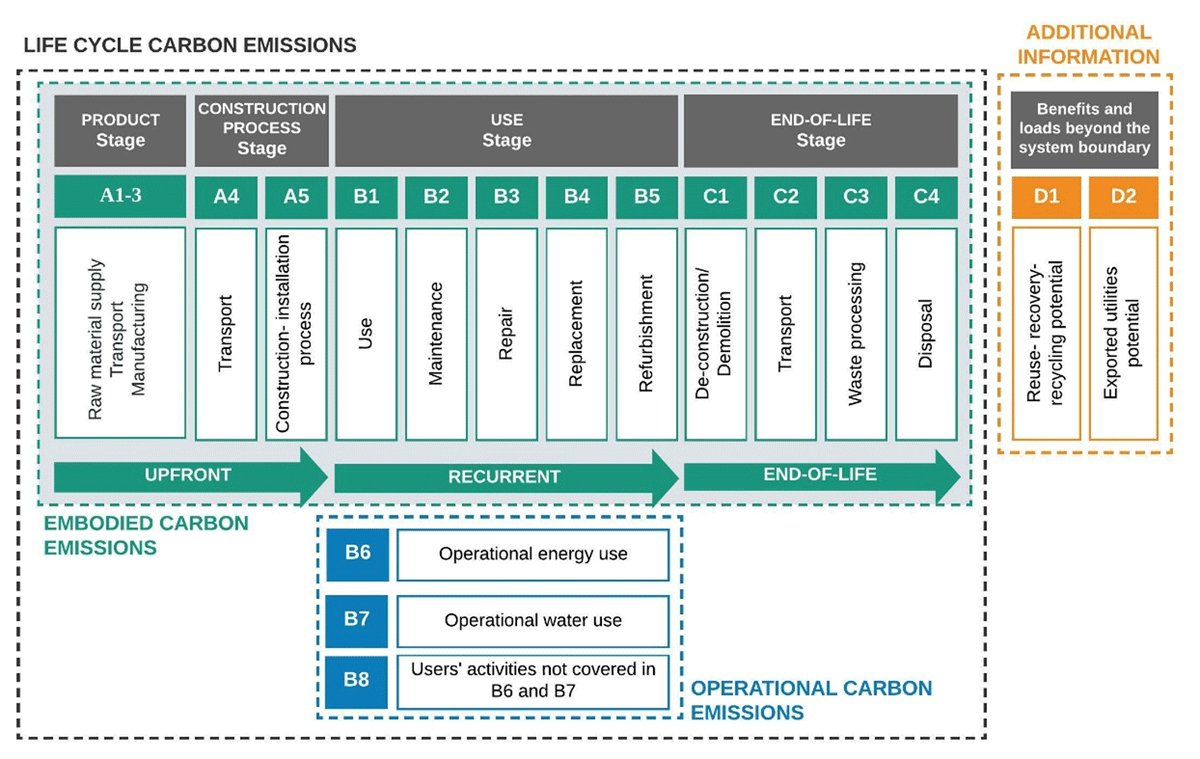
Green concrete
Structural components like columns, beams, walls and floors have a significant impact on the embodied carbon of buildings. We aim to industrialise the building process as much as possible and use concrete precast elements for structural components, prefabricated by C-concrete.
In 2018, C-concrete used 70% CEM I and 30% CEM III cement for our precast concrete elements. CEM I contains 100% cement clinkers which results in significant CO₂ emissions. To reduce these emissions, we made it a top priority to reduce the cement clinker level in the cement compositions that we use at C-concrete.
Over the past years, we have conducted intensive research and testing to develop alternative concrete mix formulas that minimise the use of cement. Our aim is to reduce the use of cement, which is responsible for 7% of the global CO₂-emissions, as much as possible.
“When we talk about ‘green concrete’, we focus on reducing the amount of cement – and therefore the embodied carbon – in our precast elements as much as possible.”
This is no fixed recipe, but a continuous improvement and commitment to keep lowering our embodied carbon in our concrete end-products.
In 2023, we successfully produced precast elements with CEM III as the main cement type, which led to a significant reduction in embodied carbon emissions.
Our current standard formula is still within the BENOR norm, which gives us a competitive edge in the market. In 2024 we will continue to adapt this formula, to decrease the amount of cement clincker even further. Starting from Q2 2024 we will produce our beams, columns and full walls with 100% CEM III/A.
We continue to reduce cement content by using alternative binders, substitute materials, additives, particle size optimizations, etc. and continuously adapting the formula of the concrete we use. Our granulate recycling installation also helps us to recover the granulates from our excessive unhardened concrete, thus reducing our concrete waste and the loss for virgin materials. Additionally, we’re optimising the local use of secondary sands and aggregates to reduce transport emissions.
In Q3 of 2023, we have installed a new silo for blast furnace slags from the metal industry, which will accelerate the production of greener precast elements. Blast Furnace slags are recycled raw materials that are used to substitute cement clinker, thus help to reduce the embodied carbon in our concrete mixtures, towards a CO2-free future.
Piloting cement-free precast elements
In 2022, we achieved a major R&D milestone by producing precast elements completely cement-free.
However, due to the lack of normative regulations for this type of concrete, it is challenging to use it in our standard buildings. Nonetheless, we have tested the performance of the elements and will continue to use the gained insights to further reduce the impact of our standard concrete mix.
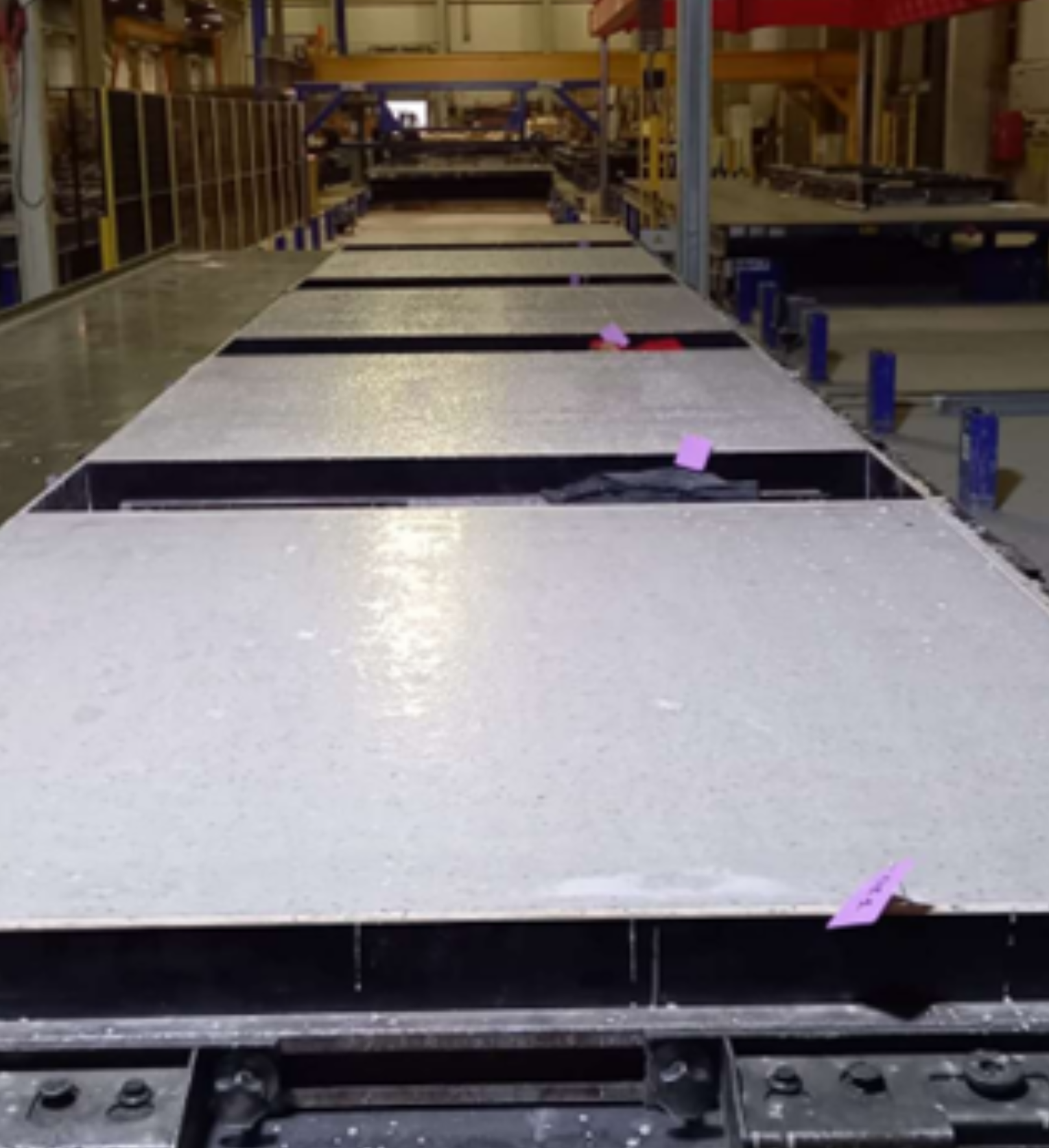
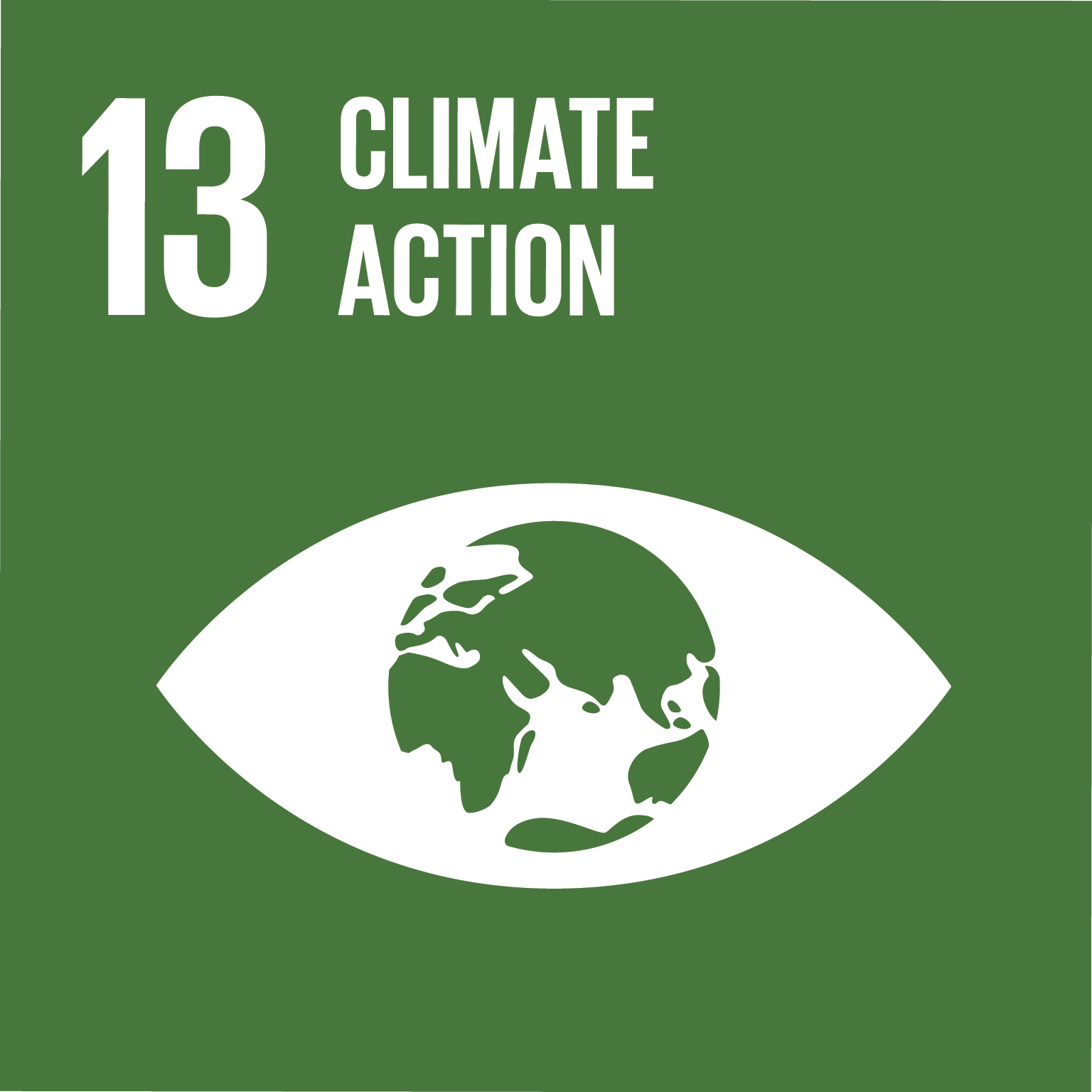
Bio-based products made from industrial hemp
C-biotech is currently in the last R&D stages of several bio-based products made from industrial hemp. In the coming months and years we are striving to accelerate the market of these kind of products by introducing traffic poles, hemp wool insulation, wooden sheets, mycelium insulation and C-hemp: the combination of wooden sheets and mycelium insulation that will act as interior wall.
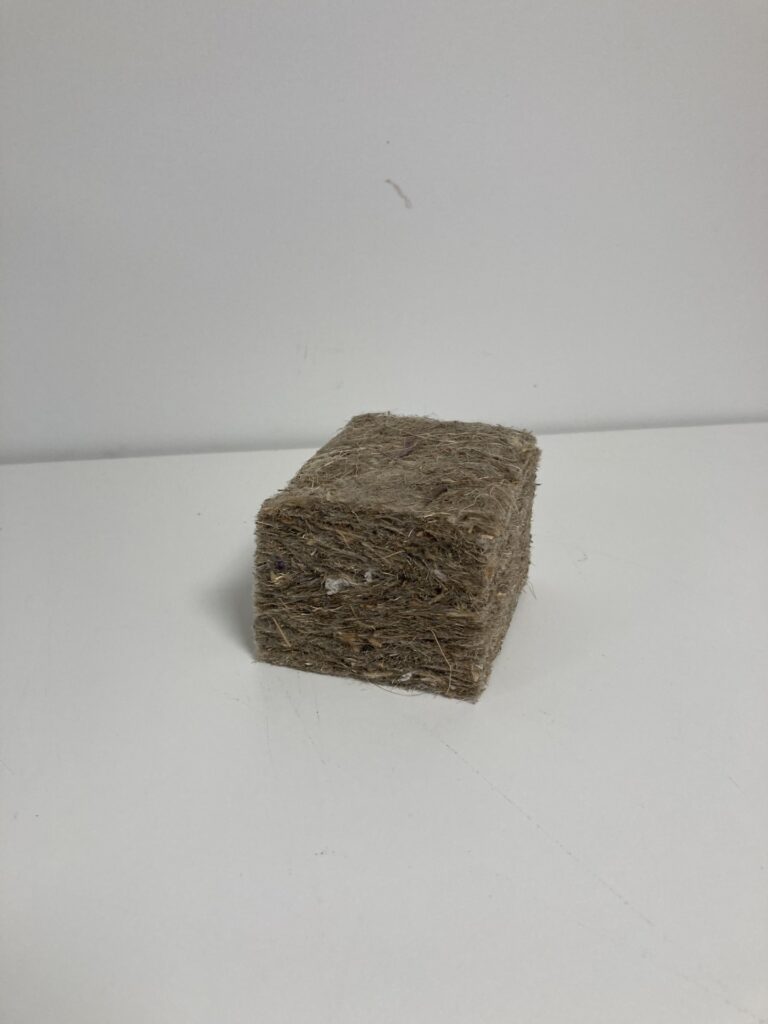
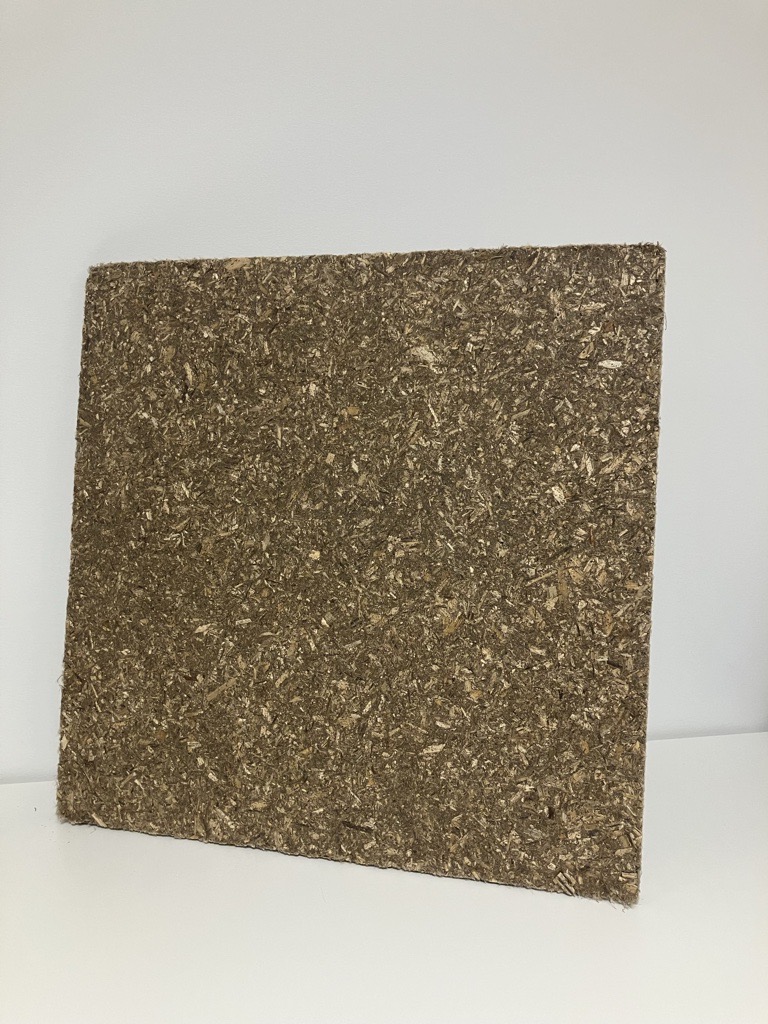
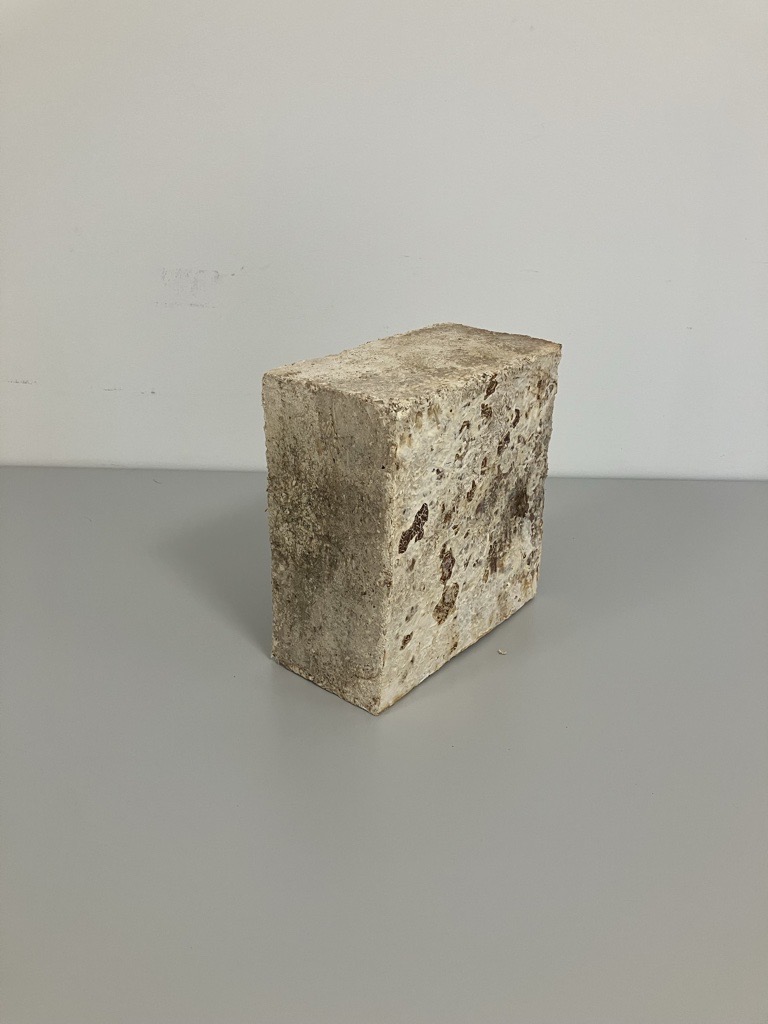
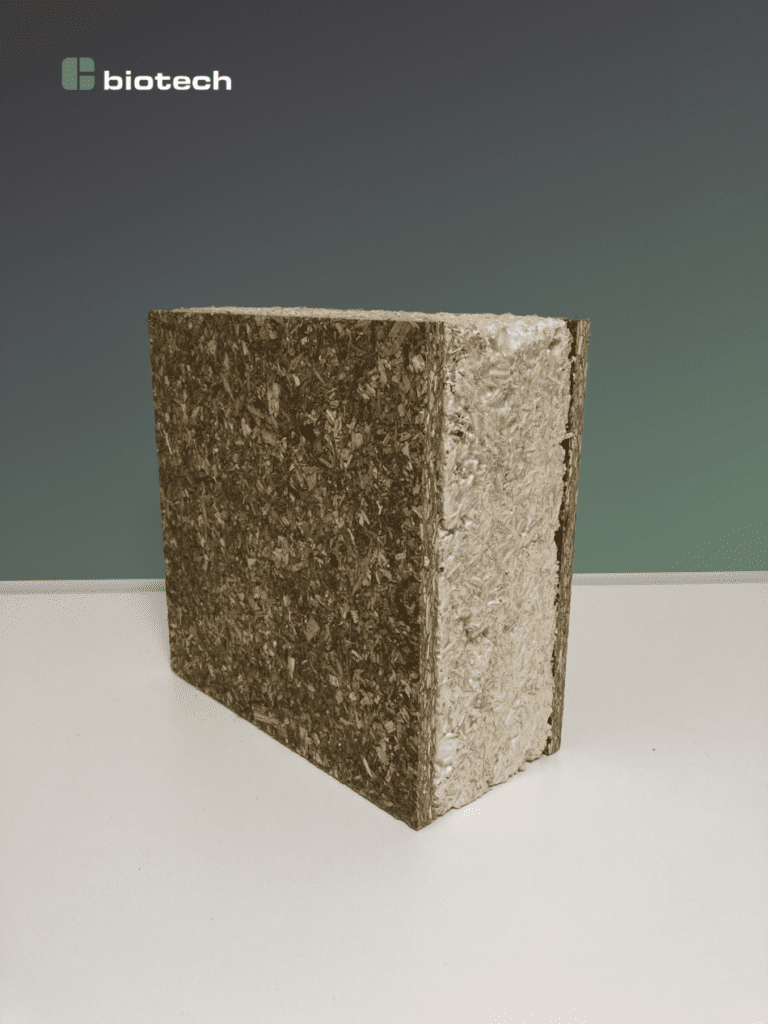
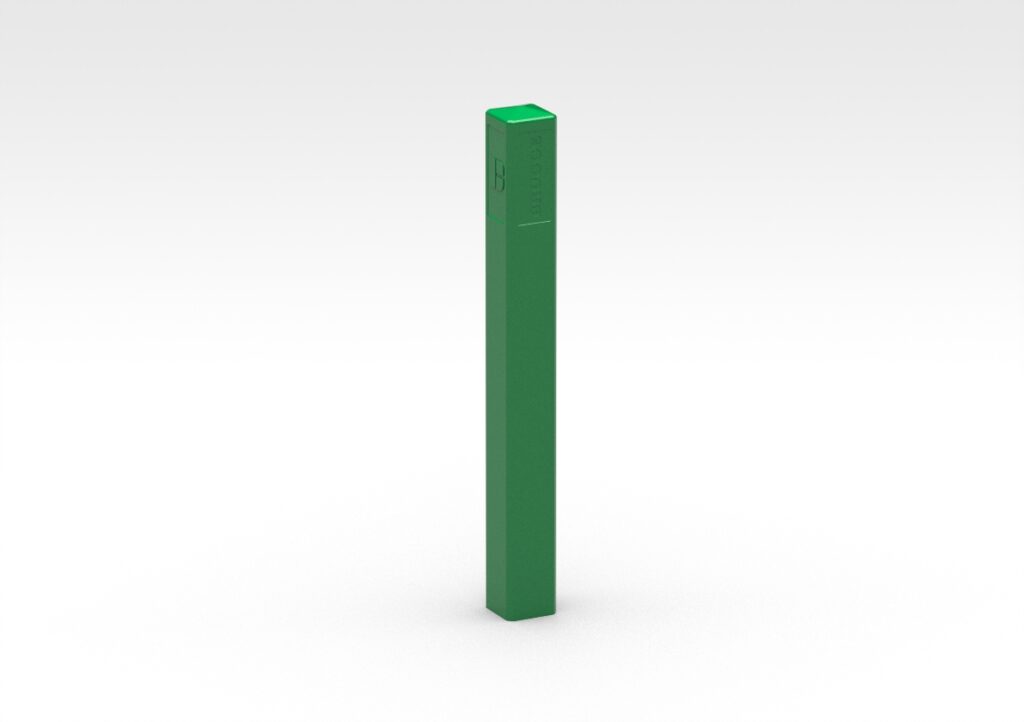
Internal focus groups
The Focus Groups are crucial to improve our impact on Cordeel Group’s most material sustainability matters. They are composed of multidisciplinary teams from different entities.
Green concrete
The focus group “green concrete” is driving the decarbonisation of our precast concrete production.
Being sponsored by Erik De Bruyn who is a member of the Board Of Directors, the team receives the necessary support to execute on the quarterly and yearly plans.
Sustainable standardisation of industrial buildings
This focus group is working on improving the standardisation of our industrial buildings. They focus on the reduction of embodied carbon and improving on design for disassembly and other circularity aspects. By making our standardisation for industrial buildings future-proof, we support our customers in their sustainability performance.
The focus group is sponsored by Isabelle Dumon, member of the management team of Cordeel zetel Temse.